高压压铸温控利器-3D打印
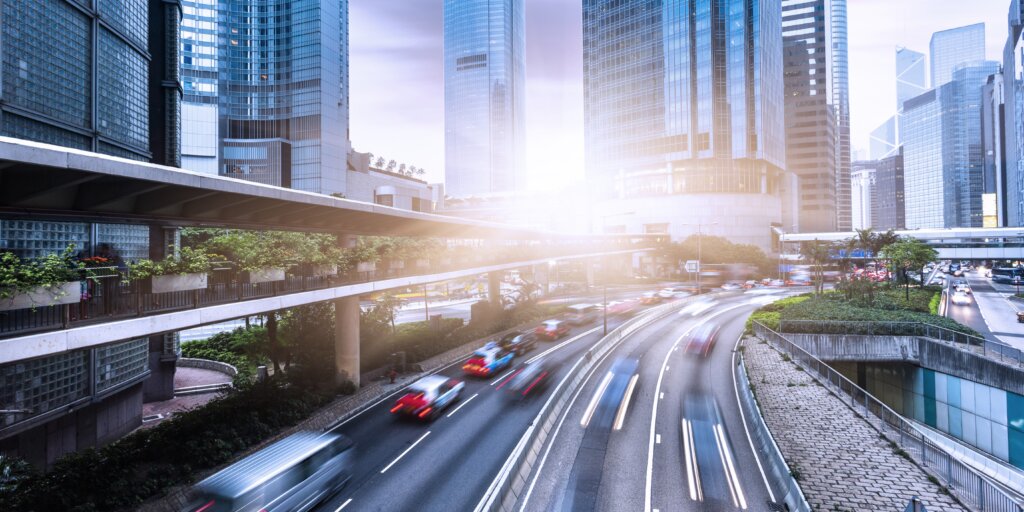
在环保和节能的大背景下,汽车制造、航空航天等行业对轻量化的需求越来越强烈。铝合金,镁合金成为实现轻量化的理想材料。特别是铝合金因具有密度低、强度高的特性,在汽车零部件制造中的应用不断拓展。以汽车行业为例,欧洲铝协发布报告称,到2030年欧洲乘用车单车平均用铝将达到 256kg。中国工信部《节能与新能源技术路线图》提出,2025 年单车用铝量目标为250kg/辆,2030年为 350kg/辆。汽车用铝合金构件中,其中压铸铝合金构件占比最高可达70%左右。从传统燃油车动力传动系统的缸体、缸盖罩,变速箱壳体,转向系统的链条盖,到新能源汽车的电机壳体,电控系统以及一体化压铸车身构件,铝合金压铸件的身影无处不在。
汽车行业迭代升级,新能源汽车产量不断攀升,市场竞争加剧,更多的部件需要高压压铸成型工艺来制造。特别是一体化压铸成型的出现,为压铸行业及压铸模具的发展带来了新的机遇和挑战。其中,压铸件的良品率及模具寿命的保证又是压铸厂及模具厂着重关注点及面临的重要挑战。压铸模具的整体热平衡管理是突破这一挑战关键的一环,其对模具的温度分布,应力控制,生产节拍和铸件中缩孔 、开裂和铸件表面质量等的管控起着重要作用。
特别是一体化压铸,铸件重量较大、形状复杂,多数铸件重量大于100kg,成型时熔融金属释放潜热大,模具温度变化错综复杂,模具各个部位温度极不均匀。靠近浇口、浇道附近端模温高,需要降温散热;产品壁厚较厚,模具难以散热的热节部位,需要重点降温;模具末端模温较低,需要合理控制热量的散失,以免造成铸件冷隔,注射不满等缺陷。
目前主要以模温机配合模具内部冷却通道,分段控制模温为主。受限于传统冷却通道的位置布局,模温的控制不能完美匹配冷却的需要。
3D打印技术能够制造出传统方法无法实现的优化冷却通道,该技术是实现模具热平衡管理的重要手段之一。3D打印技术制造出的带有异形水路的模具镶件,为压铸模具提供独特的竞争优势,在压铸领域应用越来越广泛。
3D打印的压铸模镶件其特点是承受热应力较大,内部冷却通道设计复杂,因此对打印粉末的性能及冷却通道的设计能力提出更高的要求。
目前较常见的3D打印粉末是1.2709(中国也称18Ni300),是一种通用性马氏体时效钢材,成分特点是C(0.03%),Si(0.1%),Mn(0.15%),Cr(0.25%),Mo(4.5~5.2%),Ni(17~19%),Co(8.5~10%),Ti(0.8~1.2%)。在3D打印过程中,具有较好的打印成型性能,但在实际压铸生产应用中存在韧性不足,热传导性不佳,容易发生黏模等不良。前期使用过该粉末的客户,不少反馈过曾有早期开裂,不满足生产预期的现象。
一胜百提供压铸模专用高性能3D打印粉末 – AM Dievar。
AM Dievar 具有极佳的韧性,优异的高温强度和热传导性,优秀的打印成型性,特别适合制造具有内部复杂冷却通道的压铸模具镶件。在对产品质量期望越来越高,生产效率提升,压铸成本不断下降的驱使下,AM Dievar在面临新挑战的压铸行业中正在脱颖而出。
热平衡管理的关键是模具内部冷却通道的设计。一胜百对冷却通道的设计秉承设计五部曲:
- 识别模具中潜在问题区域;
- 根据基本的设计原则进行冷却通道的设计;
- 模拟分析,如热平衡分析、热应力分析;
- 根据模拟分析结果,优化冷却通道设计;
- 优化后再分析。
正是凭借独特的高性能压铸粉末及设计五部曲,一胜百的3D打印技术解决方案呈现出明显的优势,包括:
- 提高压铸件质量,降低废品率:模具具有更均匀的温度分布,不存在局部热节,压铸件壁厚较厚位置也能得到很好的冷却,压铸件质量一致性更好;
- 模具寿命更长:模具应力分布得到优化,模具抵抗开裂的性能更佳,不会出现早期开裂现象;
- 降低维护需求:降低因模具损坏导致的停机和维护成本。
这些优势在实际压铸生产应用案例中均有体现,如下是一胜百的3D打印技术解决方案的成功应用案例:
案例 1:
某大型压铸生产企业,在生产一款新能源汽车电控柜时,压铸件局部面临严重的粘着问题,产品表面质量不良,内部疏松导致产品气密性不足。传统模具制造工艺无法有效解决此粘着问题,压铸生产过程中需要不断停机,进行手工打磨,产品不良率居高。
经一胜百提供3D打印技术方案,使用AM Dievar打印的镶件后,彻底避免原来每个班次都需进行手工打磨,提升产品良率5%以上,单件生产成本降低至原来的35%左右。
案例 2:
某汽车部件生产企业,在压铸生产一款发动机废气再循环系统部件时,因产品局部冷却的需要曾采用过3D打印镶件,镶件约5-6万模次便产生开裂现象,未达到企业生产寿命的预期。
一胜百经对模具进行分析,优化技术方案,采用AM Dievar打印的模具镶件寿命提升40-50%,单件生产成本降低至原来的50%,且模具达成产品的生产批量需求。
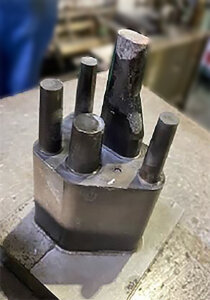
案例 3:
某压铸生产企业在生产一款发动机部件,产品批量大,质量要求稳定。 为达到缩短生产周期的目的,曾采用过3D打印1.2709制作分流锥,提升了生产效率。 但只生产约1.2万模次,分流锥局部产生开裂,无法再继续使用。
一胜百利用冷却通道设计五部曲,优化冷却通道的设计,并采用AM Dievar制作该分流锥,目前已经生产超过3.5万模次, 未发生失效且正常运作中。得益于AM Dievar较高的热传导性能,客户的生产效率得到进一步提升。目前一胜百3D打印的AM Dievar分流锥在亚太地区已成功获得客户量产验证,某一特定用户AM Dievar分流锥寿命均达20万模次以上。
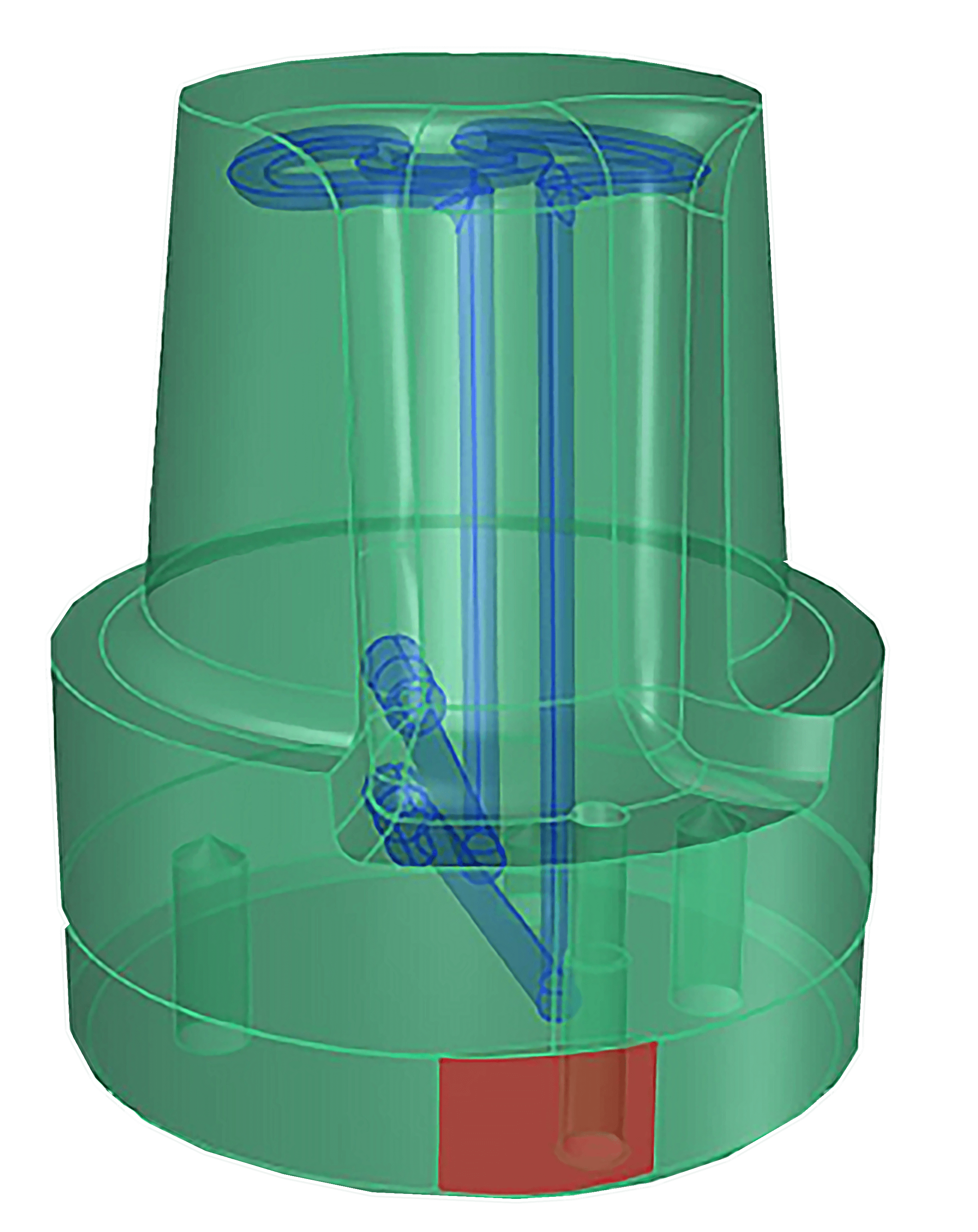
以上案例展示出一胜百3D打印技术解决方案在提升产品质量、生产效率,以及降低生产成本中的潜力。
同时3D打印技术创新的应用还可推动可持续发展,实现环境目标。
在一胜百成功应用的某一分流锥案例中,通过3D打印技术缩短生产周期10%,可实现减少12吨二氧化碳的排放。采用该技术,企业在保持竞争力的同时,也为环境保护做出贡献。
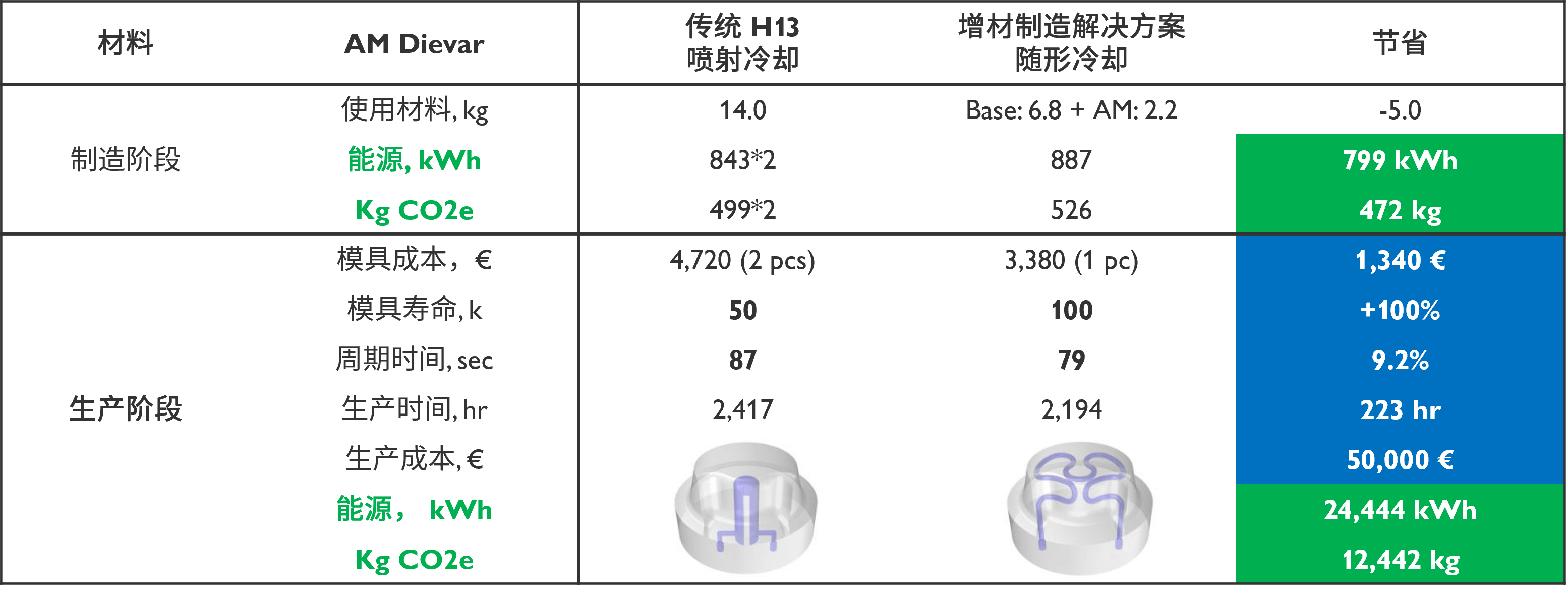
参考资料
- 《一体化压铸给大型压铸模具制造带来新机遇》http://www.cqmjxh.cn/newsx.asp?id=1372&fid=6&lm=19
- 欧洲铝协乘用车用铝量研究与预测报告(2022-2030)世铝网
- 革命性压铸技术:通过3D打印,实现3000欧元投资转化为45000欧元的年度节省