ABP
As a one-stop solution for tooling customers, at ASSAB we constantly enhance our service portfolio in the automotive, electronics, home appliances, packaging and construction industry. For improved tooling economy and increased productivity, ask for our range of ASSAB tool steel with ABP.
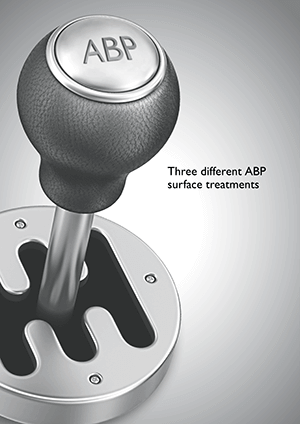
ABP is a patented shot peening process that introduces compressive stress to material surface to improve hardness and thereby reduce the risk of surface defects leading to fatigue cracking.
Other benefits induced through ABP include a reduction in thermal fatigue, heat checking, wear and in the growth of initialised cracks; improved surface finish; and extended die life by 30 to 40%.
Ongoing research and development of the ABP technology at ASSAB continues to improve the productivity, the latest being ABP Plus and ABP Dual Plus. ABP Plus, widely applied to new dies, is a combination of three processes – blasting, gas nitriding and oxidation. Our premium process, ABP Dual Plus is a combination of ABP Plus and shot peening to optimise special die casting dies that require higher tool life in excess of 100,000 shots.
The ABP range of treatments can be applied to both new and used dies, and has experienced great success in dies for die casting for aluminium, magnesium and zinc alloys, as well as dies for hot and cold forging.