Plastic Mould Tool Steel Selection for High-Volume and High-Precision Polymer Optics
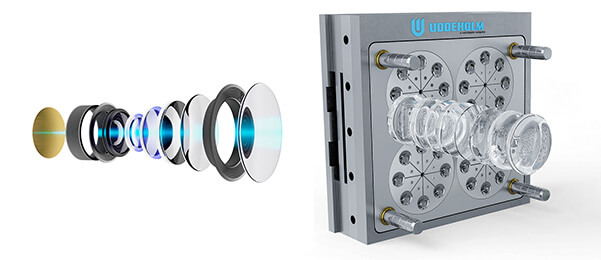
Polymer optics are crucial in modern high-tech devices and their demand is steadily increasing. Key markets driving this growth include the automotive industry, sensors, information technology, and medical applications, where lightweight, high-performance solutions offer substantial economic benefits. Examples of products benefiting from precision polymer optics include head-up displays (HUDs), head-mounted displays (HMDs), optical components for AR and VR devices, camera lenses, and transparent polymer components for medical devices.
The choice of tool steel for moulds greatly influences the surface finish, dimensional stability, and longevity of the mould. For optical-grade components, it is crucial that mould materials are highly polishable to achieve a mirror-like finish with good dimensional stability. Additionally, using corrosion-resistant tool steel is vital when working with corrosive polymers to prevent mould degradation and ensure consistent production.
Beyond polishability, high wear resistance is critical for maintaining precision over extended production runs. High-volume manufacturing requires tool steels that can endure the repetitive stresses of injection moulding without compromising dimensional accuracy. Tool steels with high wear resistance not only ensure consistent output but also minimise maintenance costs while preserving the integrity of complex surface patterns and fine details in the final polymer parts.
Choosing the right tool steel for high-precision polymer optics is vital for balancing surface finish, durability, and cost-effectiveness. This careful selection enables manufacturers to meet the growing demand for advanced optical products across various industries, ensuring optimal performance and reliability in high-volume and high-precision applications.
ASSAB suggests matrix-type tool steel such as Tyrax ESR and Unimax to satisfy the high requirements for surface finish and mass production. The working hardness of both Tyrax ESR and Unimax is 54-56 HRC, which will significantly increase mould life. Their special alloy design removes most of the primary carbides and reduces carbide size, contributing to excellent polishability. Tyrax ESR contains a high amount of chromium, as it is corrosion-resistant steel. Unimax is modified 5% Cr steel with excellent toughness.
Chemical composition:
C | Si | Mn | Cr | Mo | V | N | |
Tyrax ESR | 0.4 | 0.2 | 0.5 | 12.0 | 2.3 | 0.5 | + |
Unimax | 0.5 | 0.2 | 0.5 | 5.0 | 2.3 | 0.5 | – |
Properties of Tyrax ESR and Unimax in plastic moulding:
Grades | Properties | Advantages | |
Tyrax | Unimax | High hardness (recommended 54-56 HRC) | long mold life, low maintenance cost, dimensional accuracy |
High strength | Resistant to deformation | ||
Good toughness | Able to handle complex mould designs | ||
High temper-back resistance | Proficient in handling high melt temperature polymers | ||
Excellent polishability | Able to achieve Mirror finish surface | ||
Corrosion resistance | Adept at managing Corrosive polymers, Corrosion in cooling channel, HFFR and Bio-composites |